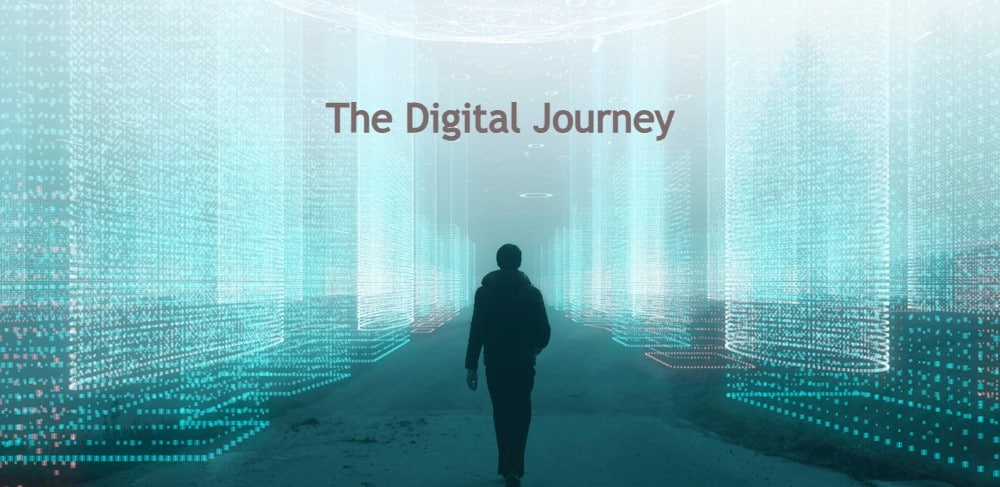
Navigating the Digital Journey – Astrix Interview with LCGC North America
Achieving digital transformation in the scientific laboratory
Advances in the digital transformation of scientific labs are occurring so fast that it’s hard to keep up—as if COVID-19 hasn’t given labs enough to keep up with already. But when you consider how much these advances help researchers improve efficiencies, tap into higher quality data and, ultimately, accelerate the launch of game-changing developments, it becomes clear that laboratories can’t afford to fall behind. Nor can they afford to take a merely “pure” approach to digital transformation, either. Successful digitalization starts with smart end-to-end strategy and prioritizes the human element. And there’s no better time begin than now—even during COVID-19.
Just ask Dale Curtis, CEO of Astrix and Bridgette Chambers, MBA, PhD, President of Outsourced Services at Astrix. In fact, we did, and we discussed digital transformation’s evolution and how laboratories can benefit, too
LCGC: Who is Astrix Technology Group?
Curtis: Astrix is a vendor- independent scientific consulting and outsourced solutions provider focused on solving complex problems that reside at that crossroads between really diverse scientific areas and domains within IT.
We are all scientists here—engineers, informaticians, architects, analysts—in the business of helping science-focused communities deploy innovative solutions that allow clients to turn data into knowledge, increase organizational efficiencies, and improve quality—ultimately facilitating regulatory compliance. Unlike traditional IT-consulting companies, Astrix is all about the science. It’s at the core of everything we do and is critical to enable us to solve those complex problems that reside in the companies that we serve.
LCGC: What does it mean to digitally transform your laboratory?
Curtis: This is a term that’s used in so many different contexts that it’s important to step back and understand that it’s not just about focusing on a micro-component of the work process in your laboratory, but about identifying and addressing a given process end to end.
So, to digitally transform doesn’t mean just bringing in a new system. It’s about looking at the complete process that experimental design comes from. It is important to remember that the goal is to remove manual processes. Specifically, you want to improve data capture throughout the entire process. Thus, any type of digital transformation is about tackling the end- to-end process rather than any single system, which tends to be a very tactical approach.
LCGC: What benefits should you expect to see from digitalization?
Curtis: Going back to my earlier point, if you are aligned strategically to impact an end-to- end process, there’re real quantifiable benefits that can come from such an effort.
One is the significant reduction in manual entry of information. You can actually measure how much time scientists spend on manual operations. Manual transcription of data from one system to another, data review and verification, preparation of reports, extraction of data: These are all manual aspects, and they present a lot of quality issues. So, digitizing these types of workflows can reduce or eliminate some of those manual transcription errors, and all of these aspects can be measured.
There are numerous published studies around this topic, and one comes to mind from the Medical Laboratory Observer. They’ve actually recorded, on average, 15% error in manual transcription during a routine analytical test1. So, think about the risk associated with this and how it can impact things like quality metrics, quality by design, and data integrity.
If you work to achieve that end-to-end digitalization, you’re able to address these types of requests a lot more efficiently.
LCGC: What is the timeline associated with a digital transformation?
Curtis: It really depends on where you start. If we think about the paths that companies follow along during the transition from traditional research to digital maturity, there’s an evolutionary process that occurs from ideation all the way through the digital journey. Most importantly, there needs to be an organizational evolution to foster this type of transformative environment, underpinned by evolutionary changes surrounding connectivity, process improvements, and the development of necessary skills to support the effort.
Companies will inevitably proceed down some path in each of these categories. In some cases, you start from nothing, and often that’s actually a better place to start from than a scenario where you have a bunch of 10-year-old systems that barely keep up with your current laboratory processes. So, if you consider an analytical laboratory doing traditional work, that’s a much more focused project that could be achieved in about a year’s time. If you are working end to end and plan to tackle significant scope, it could take several years.
So, it goes back to that first question: How big is the end-to-end scope that you have identified? But don’t underestimate the time and significance of an effort like this, regardless of the scope. It’s more than just buying a system from a vendor and plunking it in.
LCGC: What are the biggest challenges to expect when starting a digitalization effort?
Curtis: That’s a good question, and these challenges involve the “people thing.” We are talking about cultural elements, changing people’s work habits, as well as their readiness to accept that kind of change, so I don’t think the biggest challenges are technical. Not that there won’t be technical challenges; there certainly will be. But they’re not the biggest challenges for companies that want to do digital transformation.
If you do an end-to-end workflow analysis, you can’t just assume that a vendor’s three-letter acronym will solve things, whether it’s a laboratory information management system (LIMS), electronic laboratory notebook (ELN), etc. Those acronyms have even lost a lot of meaning in the last 5–10 years. There used to be a real difference between ELN and LIMS, but that’s no longer true. Some people think they need a LIMS to do what would be better suited to an ELN, or they try to transform these systems to behave in certain ways they were never built to behave.
Another challenge is just navigating the landscape of so many different solution or “platform” providers pitching silver bullets to achieve digital transformation. And it just doesn’t work that way.
So, yes, there are technical challenges, but the biggest ones involve altering the working habits of your organization.
LCGC: Given the disruption and uncertainty associated with COVID-19, why not delay or pause your digital transformation?
Chambers: This is definitely a point that many organizations are making. They find it prudent to push projects into the future, in an attempt to save a bit of money. But I would argue that this is a short-term strategy for companies basically trying to survive.
For companies that want to thrive, however, investing in digital transformation increases their competitiveness and, in fact, helps them be more agile during uncertain times, such as those we find ourselves in.
And while I think we could write an article solely on why laboratories should prioritize the digital transformation, instead let me highlight three trends that support prioritizing your digital transformation now. COVID-19 clearly illustrates the need for workers to be more connected than ever. And the digital transformation allows people to leverage more technologies, more feedback loops, and much more information—in other words, it enables people to be more successful and more productive in real time.
Secondly, we all see technologies continuing to explode and abound. This creates opportunities for companies to address demand for their customers, not only at a macro level, but at a micro level as well. You have more stock-keeping units, more product variation, and a lot of customization. When supporting this much change, it can create havoc in manual systems. Digital transformation takes advantage of automation and smart technology, which connects people and machines far more productively.
Lastly, there’s an ever-increasing gap in skilled labor. A study recently published by Korn Ferry predicts that by 2030, the talent shortage will reach more than 85 million people2. So, we’re talking about a big need for hard-to-find people. Digital transformation creates the opportunity to support remote teams and be much more flexible and effective with human capital.
LCGC: How can Astrix assist laboratories with their approach to digital transformation?
Curtis: Again, we are an independent, vendor-agnostic consulting company. And as Bridgette alluded to in her response, we are focused less on technology and more on people, work processes, and work practices, with scientists that will work side by side with you in the laboratory to solve these problems.
It’s best to step back and figure out the meaningful changes that need to happen, the best fit for the work process, and the requirements to make that change happen. Digital transformation starts with clear objectives and tangible goals that include defining true end-to-end work processes, and these can produce tangible outcomes in reasonable time frames.
For example, it can be done in a single laboratory, like an analytical component in a larger company. Identify an analytical step within that laboratory in which a chemist submits essential materials for characterization. That’s a bite-sized piece, but it’s a workflow that you can map out end to end. Simply put, keep it end to end, don’t break it down any further, and pick a starting place. And that starting place could be in the middle.
Once you get a piece mapped out, it allows you to move in either direction. Astrix is staffed with the right mix of science and expertise to help you navigate whatever digital transformation journey you are on, no matter how big or small the program.
References
- F. Tieman, “The Role of Lab Automation in Reducing Diagnostic Errors,” Medical Laboratory Observer, Sept. 21, 2017, www.mlo-online.com/information-technology/lis/article/13009260/the-role-of-lab-automation-in-reducing-diagnostic-errors, accessed Aug. 18, 2020.
- Franzino, et al., “The $8.5 Trillion Talent Shortage,” Korn Ferry, www.kornferry.com/insights/articles/talent-crunch-future-of-work, accessed Aug. 18, 2020.
Case Study: LabWare Centralized Data Review for a Global Biopharmaceutical Company
Overview A global biopharmaceutical company specializing in discovery, development,... LEARN MOREWhite Paper: Managing Data Integrity in FDA-Regulated labs.
New White Paper LEARN MORELET´S GET STARTED
Contact us today and let’s begin working on a solution for your most complex strategy, technology and staffing challenges.
CONTACT US